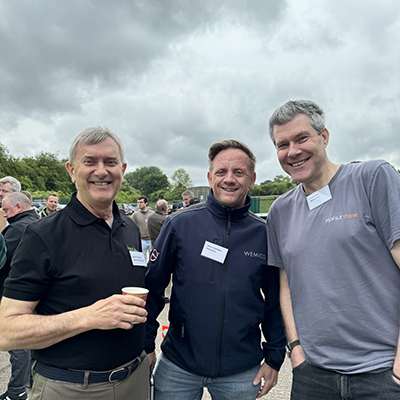
News
View our latest news to stay up to date with our recent developments.
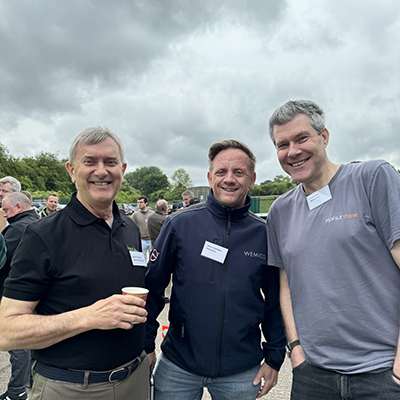
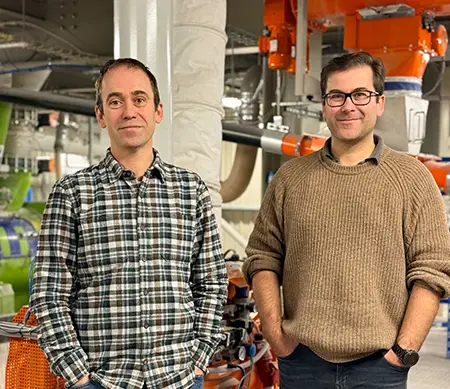
Lime Green Invests in Plant
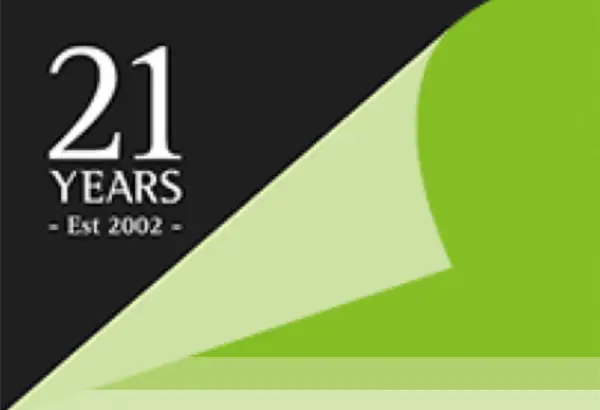
Lime Green turns 21
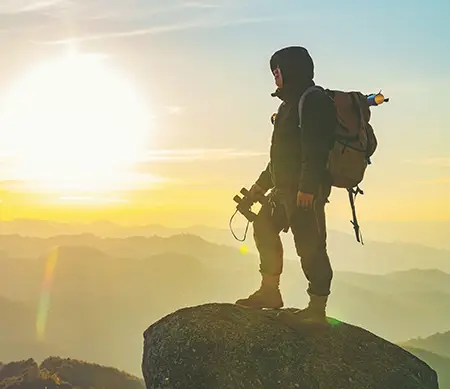
LG21: Andy Mitchell from Avad Consulting Q&A
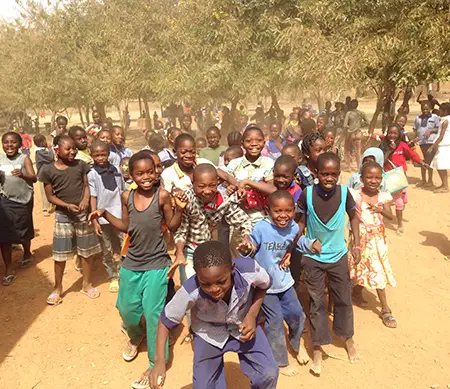
LG21: Will Kirkman from Ecomerchant Q&A
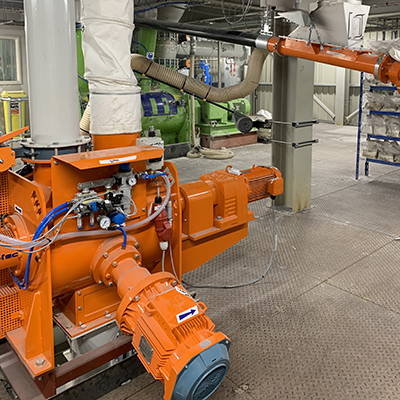
LG21: Ian Shaw from m-tec
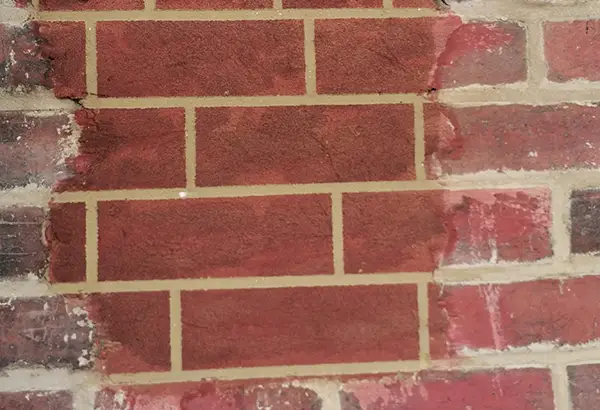
LG21: Ian Womersley from Womersley's Q&A
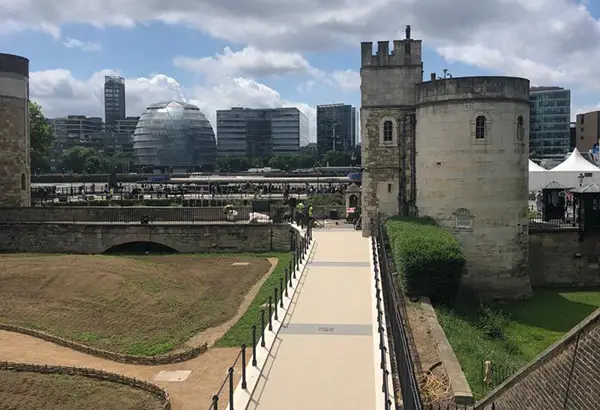
LG21: Derek March from Brick and Lime Supplies Q&A
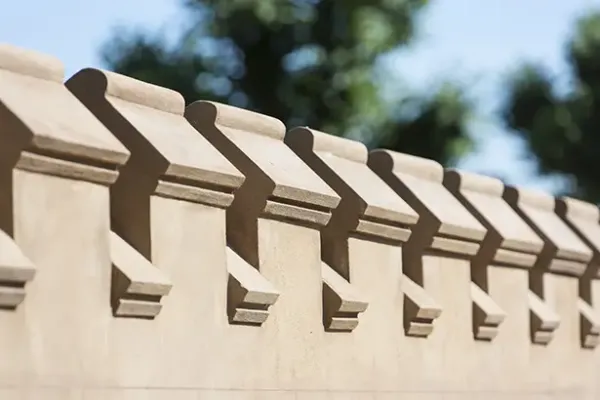
LG21: Michael Tincknell from AVV Solutions Q&A
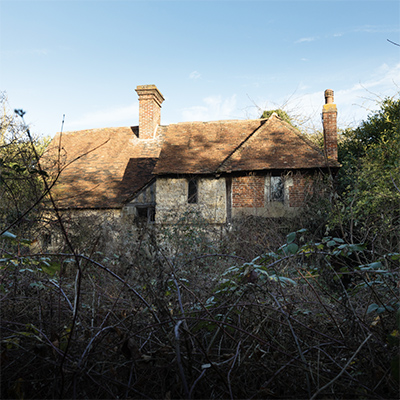
LG21 Jonathan Garlick from SPAB Q&A
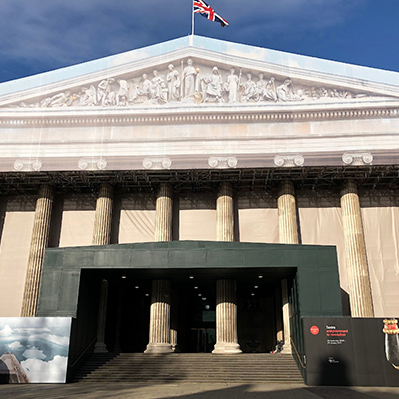
LG21 Russell Brewis Artisan Plastercraft Q&A
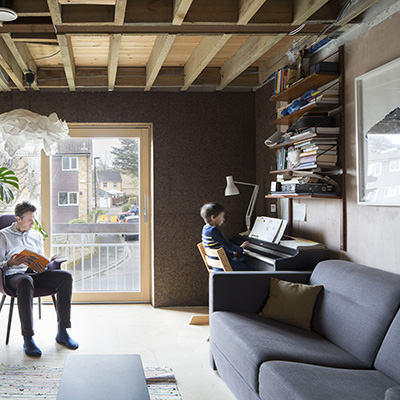
LG21: Harry Paticas from RAFT Q&A
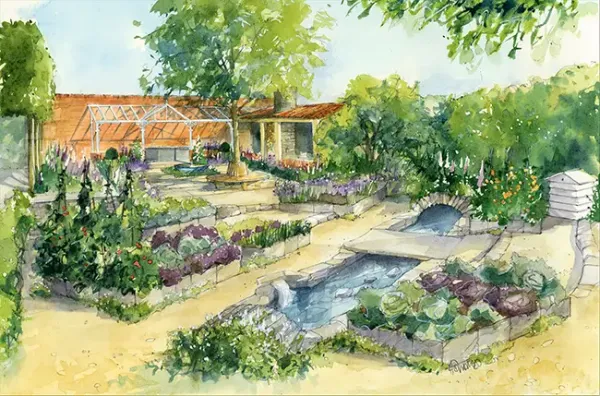
Chelsea Flower Show: Using Lime in the Garden
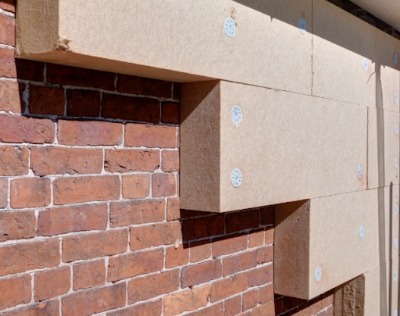
The Benefits of External Wall Insulation
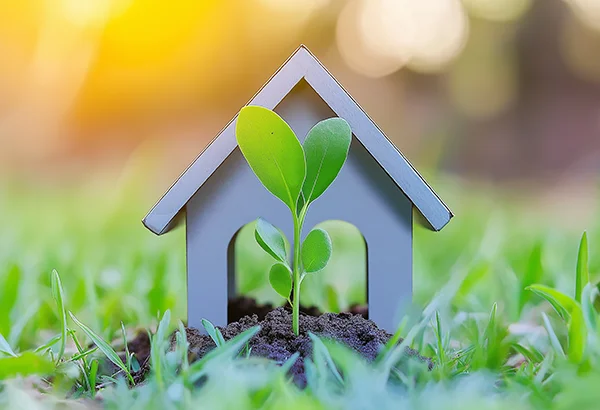
Why Use Healthy Building Materials?
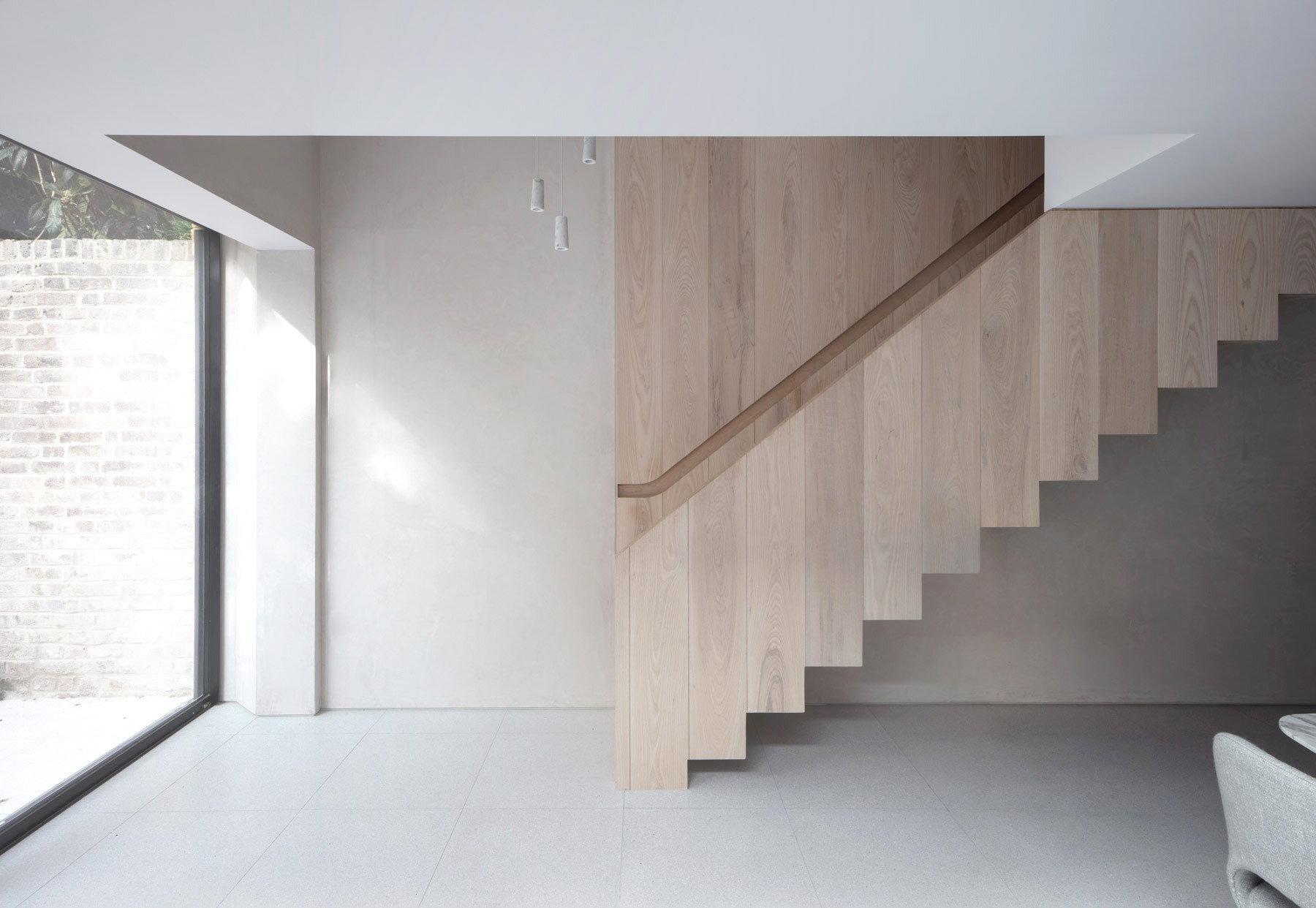
Solo Lime Plaster Is Featured In The Times!
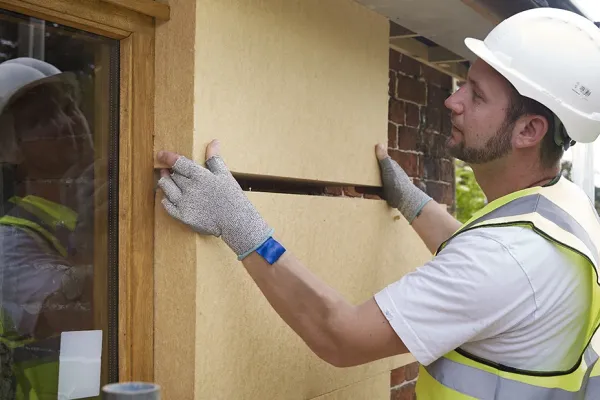
Internal Wall Insulation Vs External Wall Insulation
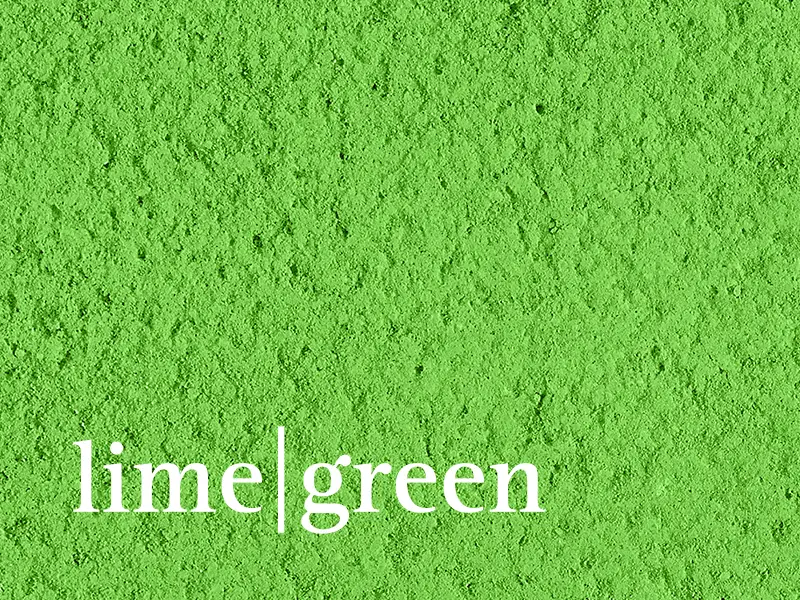
Construction: how can we reduce our reliance on plastics?
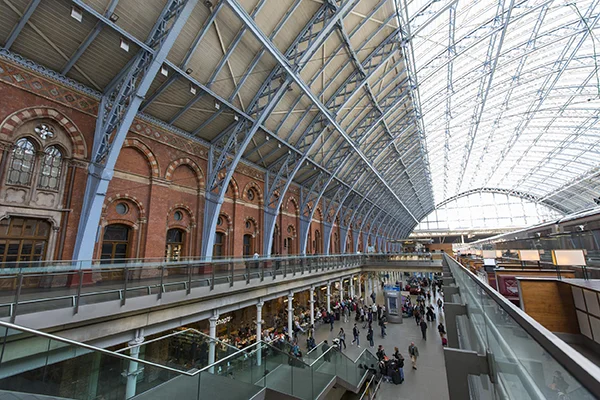
Top 12 Interesting Lime Buildings and Structures
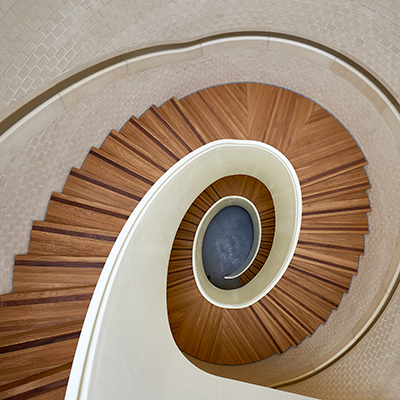
Lime Green's mortars used on RIBA Stirling Prize winning gallery
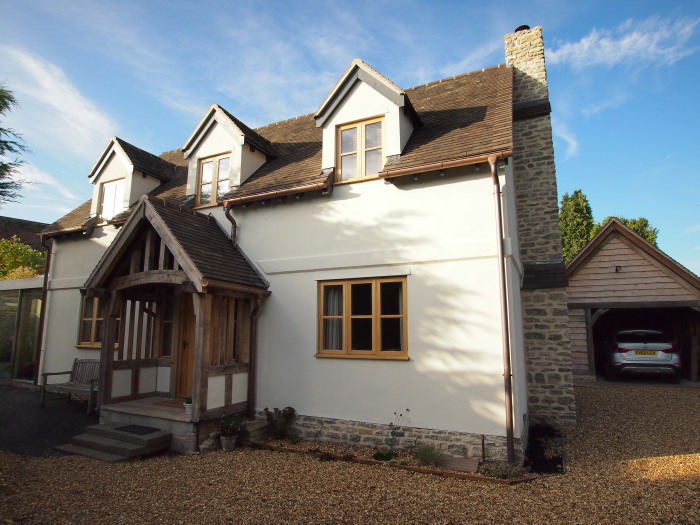